Using Integrated Software Solutions to Manage Pharmaceutical Product Labeling Deviations
Pharmaceutical product labeling deviations can be hard to manage manually. Let’s look at how integrated software solutions can help.
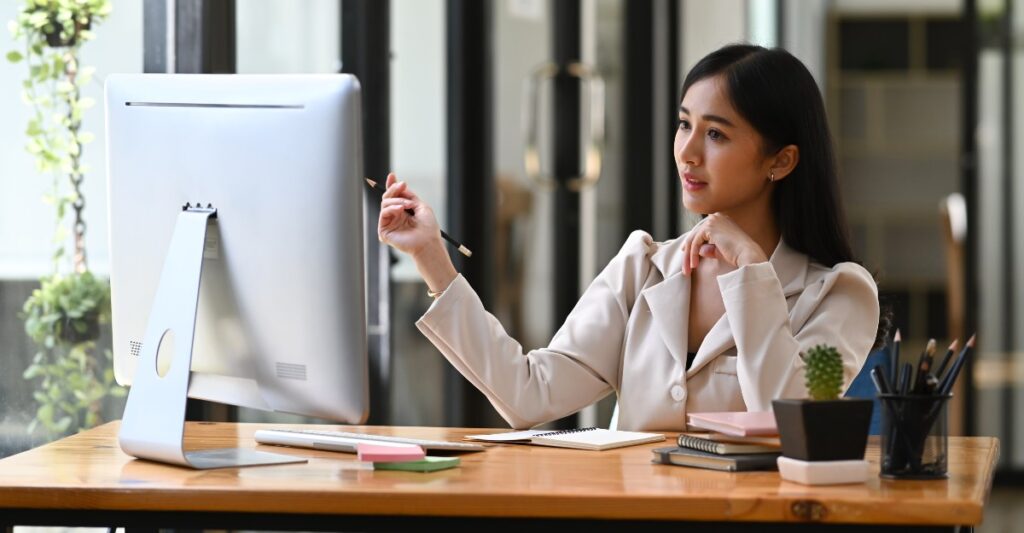
Labeling deviations are business-as-usual for pharmaceutical companies with products marketed across the globe. Maintaining labeling compliance is vital to your business—far too important to leave to multiple systems that don’t talk to each other in a matrixed, global environment.
Information silos can result in compliance problems, delays, and inefficient re-work. When critical core information about a marketed drug product changes – generating a label deviation – business demands a robust response that maximizes efficiency across all functional areas.
But before we go any further, let’s lay some groundwork by defining labeling deviations.
What is a Labeling Deviation?
As long as a drug product is being used, new data about the product are being created and reported. When that data constitutes any difference taken from the company’s Company Core Data Sheet (CCDS), or its core understanding about the characterization of the drug product and how it is labeled and represented to the marketplace, compliance requires updating the label and submitting it to avoid the regulatory pitfalls of being inaccurate, false or misleading.
For example, every drug marketed in the U.S. needs to be submitted to the FDA for approval. During that approval process, it’s possible that the FDA doesn’t agree with the wording on the label. The pharmaceutical company and the FDA will negotiate and come to an agreement on wording that differs from what’s in the CCDS. Once the submission is approved, the deviation is marked as a labeling deviation in the pharmaceutical company’s system.
Labeling deviations commonly occur throughout a product’s lifecycle, so managing them requires business systems that retain, track, implement and communicate updates across functional areas.
So, Should All Labeling Deviations Be Treated the Same Way?
Definitely not! For example, you wouldn’t want to treat a safety change the same way as a non-safety change. That’s because the timelines associated with a safety change are much tighter, especially when a high level of severity is involved. Meanwhile, a non-safety change like a formatting change would be less severe, so more time is allowed.
There are two main types of labeling deviations: content and timeline.
Content Deviations
A content deviation takes place when the language used on a local label differs from what is stated in the CCDS. For instance, the CCDS may specify that the drug could cause your hair to turn blue, while the local authority may prefer wording indicating that your hair could become blue or green. From there, the pharmaceutical company can decide whether they want to make this change for every single market where the drug is marketed.
Timeline Deviations
A timeline deviation happens when a pharmaceutical company is unable to meet its defined SOP for a given step in the submission process. For example, internal timelines are driven by company SOPs and they’re not regulated by health authorities. For a safety change, companies strive for a 30-, 40-, or 45-day timeline.
Let’s say an SOP gives the company 30 days to submit to a health authority. If the company’s regulatory team realizes on Day 20 that they won’t make it in time, they can ask for a timeline deviation from the company.
External timelines come from regulatory authorities like European Medicines Agency (EMA). As an example, Module 9 is a system developed by the EMA to electronically submit and review applications for the authorization of medicinal products. If Module 9 dictates that a timeline needs to be faster than an internal timeline, pharmaceutical companies need to adhere to the external timeline in order to remain in compliance.
How Can a Company Prioritize Its Deviation Response and Remain In Compliance?
An integrated software platform that crosses functional levels in the company is an essential compliance tool. The software should track changes and approvals as the content deviations are resolved and provide controls to ensure that when local regulatory label changes are submitted, the timeline deviation loop is closed and appropriate functional areas notified.
How Can Pharmaceutical Label Tracking Software Reduce Noncompliance Risk?
Pharmaceutical label tracking software is a robust total labeling management system that incorporates deviation management. Its tracking function drives clear procedures for reporting, investigating, and resolving deviations.
Labeling information risk management involves adherence to SOPs throughout the documentation lifecycle. Each stage, from creation to archival, can be customized to specific business needs, while following local market regulatory requirements. It is a centralized repository that tells managers and team members where things stand with labeling deviations.
The system can generate reports on deviations over a given period to help identify trends, exceptions, and dependencies in different markets. It facilitates quality review and corrective action planning by providing an audit trail at every stage of documentation.
The notification and communication capabilities keep deviation resolution processes moving forward, cutting through those silos. This elevated responsiveness across the organizational matrix reduces labeling lifecycle risk by directing change creation, implementing, internal approval tracking, inspecting for multi-lingual content and artwork updates according to company-determined business rules and SOPs.
Conclusion
Pharmaceutical product labels are living documents that require changes and updates during their lifecycle as new information about safety becomes available, or if manufacturing changes occur. In addition, they are tightly regulated documents—that is, their precise verbal content, graphics, and artwork have been approved by regulatory authorities in countries and local regions to permit the drug product to be marketed there. So when labeling deviations occur, it’s necessary for pharmaceutical companies to track these changes to ensure compliance.
Tracking Portal by Intagras reduces information silo risk through a robust notification and communication system while driving deviation resolution forward. Tracking Portal ensures end-to-end labeling process management from the core company data sheet (CCDS) to local regulatory approval timelines. Contact us to learn more about this solution.
Need labeling deviation help? Talk to us.
Have questions? Need more info? Talk to one of our experts or request access to our Tracking Portal today.